Chassis Pools: A Brief Background
The method in which chassis are provided in the United States as compared to other countries is very different. The typical model used outside the United States was based upon chassis being owned and operated by the motor carrier. In the US, as part of their service offering, shipping lines developed a different approach where they provided chassis to motor carriers to move containers over the road. In the early 1990's ocean carriers looked for ways to operate their chassis more efficiently, resulting in "Chassis pooling". Chassis pooling allowed for the lines to share their chassis and improve the efficiency of the supply chain.
Prior to CCM's inception, shipping lines typically had their own chassis to put under their own containers. As such, there were many different operating theories and was a disjointed approach to chassis provisioning in the United States.
Chassis pooling evolved into many forms over the next 15 years, including terminal pools, alliance pools, and interoperable pools. In 2005 the ocean carriers, under OCEMA, decided to take a more holistic approach to chassis pooling and created CCM to be the manager of their interoperable chassis pools.
It was realized through pooling, chassis could be operated at a 25% less asset base than what had originally been in place for moving cargo containers. There were operational synergies gained through a more efficiently run chassis operation materializing in a reduced carbon footprint As lines began to divest themselves of their chassis selling them to leasing companies, ocean carriers began to shift away from providing chassis for their shipments, making way for new models. And as ocean carriers further disengaged from chassis, the Shipper/motor carrier became increasingly responsible for providing chassis.
Chassis pools enable intermodal participants including ocean carriers, motor carriers, leasing companies, shippers, and more to access container chassis under one focused management at the lowest possible cost. In CCM pool models, where pools are modeled after interoperability, anytime a container comes off a train or a ship, it can use any chassis available in the network and motor carriers have the option of using that chassis freely within the network.
Chassis models in the US
CCM's Chassis Pools
CCM Pools are managed to operate the most efficient and effective chassis models for all stakeholders through the following principles:
Fully Interoperable – following a fully interoperable fleet management philosophy driving maximum efficiency.
Service Quality – providing Safe and Reliable Chassis to get the job done
Availability– having the right chassis in the right place at the right time
Flexibility – providing assets across a wide network of operating facilities
Operational Efficiency– focused, reliable and consistent process execution across the network
Environmental Sustainability – best operational efficiency driving the lowest carbon footprint
Focused Management – via a single point of contact, providing objective business execution and impartial decision making
Chassis Pool Benefits:
"Maximize availability, utilization and value"
"Minimize redundancy, congestion and waste"
Terminals: are able to reclaim scarce acreage by reducing the number of chassis stored
Motor Carriers: are able to transit a terminal more quickly, while obtaining a well-maintained piece of equipment
Ocean Carriers: customers benefit from a more consistent and reliable equipment supply
By utilizing chassis from CCM Pools you can access chassis under one focused management at the lowest possible cost. A pool enables operating savings to be achieved by:
- Reducing the combined inventory levels
- M&R economies of scale
- Reduced repo expense through pool members' synergies
Service and equipment availability are core values at CCM. CCM understands the impact that a lack of chassis availability can have on all parties in the supply chain as well as the related operational costs. CCM works closely with its terminal partners and members to forecast volumes and ensure that equipment is available to efficiently handle bookings and manage terminal fluidity. CCM's track record on service over the years has been impeccable due to their focus on equipment availability.
CCM Quality
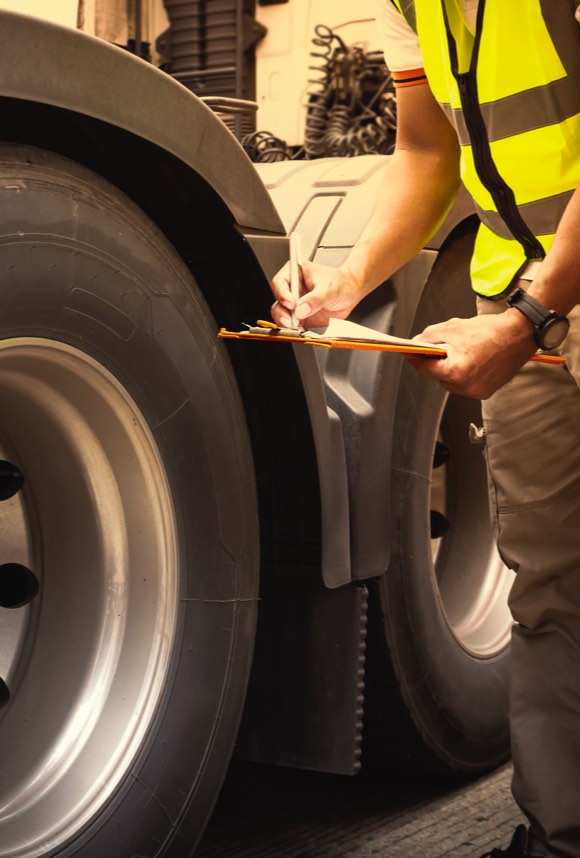
- Heavy focus on hiring experienced maintenance and repair inspectors
- Extensive training of associates
- All M&R inspectors are IICL certified (either hired or certified shortly thereafter)
- Strict adherence to FMCSA repair guidelines
- Annual preventive maintenance inspection
- Systematic full chassis inspections occur at time of each repair
- Premium maintenance system that tracks and monitors all repair related events
- Frequent audits of vendors to include their service vehicles, tools, work space, and certifications
- Extensive vendor auditing(pre/post) and annual vendor recognition awards and events
- Active partner in designing the latest in chassis parts with major manufacturers
- Active members and committee participants in both IANA and CVSA
Interoperability in Chassis Pools
The beginnings of interoperability
15 years ago, CCM was created by the ocean carriers equipment management association (OCEMA) to manage chassis on behalf of ocean carriers and drive momentum synergies into the chassis operation. Prior to CCM's inception, every line had their own chassis to put under their own containers. There were many different operating theories – it was a disjointed approach
CCM was designed to be a collaborator and bring stakeholders together into a network to ensure all stakeholders were given an opportunity to operate in an efficient way. It allowed for a chassis fleet to exist in numerous parts of the country where anytime a container comes off a train or ship, it can use any chassis available in the network and motor carriers have the option of using that chassis freely within the network. It was realized through pooling, chassis could be operated at a 25% less asset base than what had originally been in place for moving cargo containers and in addition to savings relative to the overall fleet size, there were operational synergies to be gained
Taken to the next level, those synergies lead to more efficiently run chassis operations, materializing in a reduced carbon footprint. These were the beginnings of what we refer to today as the interoperable chassis pool network.
CCM defines Interoperability of chassis as when the motor carrier may select any chassis within the pool network, regardless of the chassis owner/branding on the side of the chassis, to transport any shipping container within the pool network.
Degrees of Interoperability within the Chassis Pool
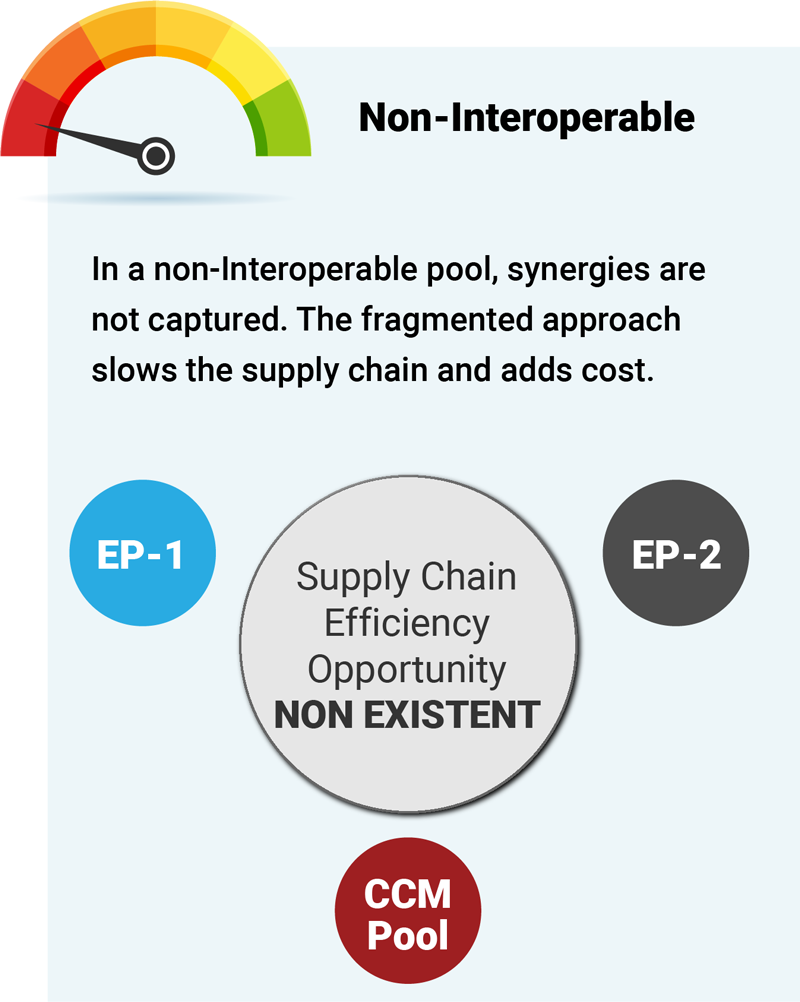
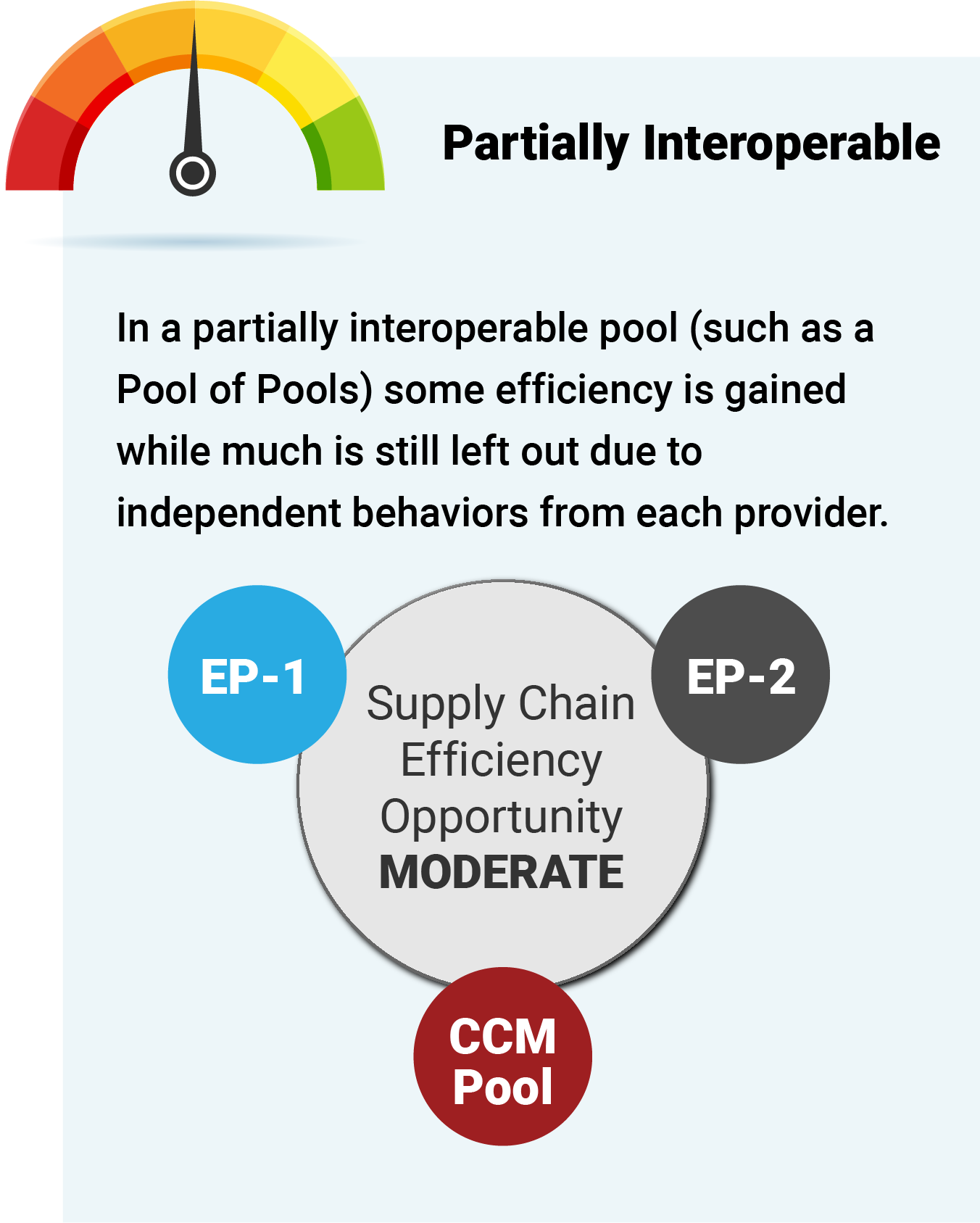
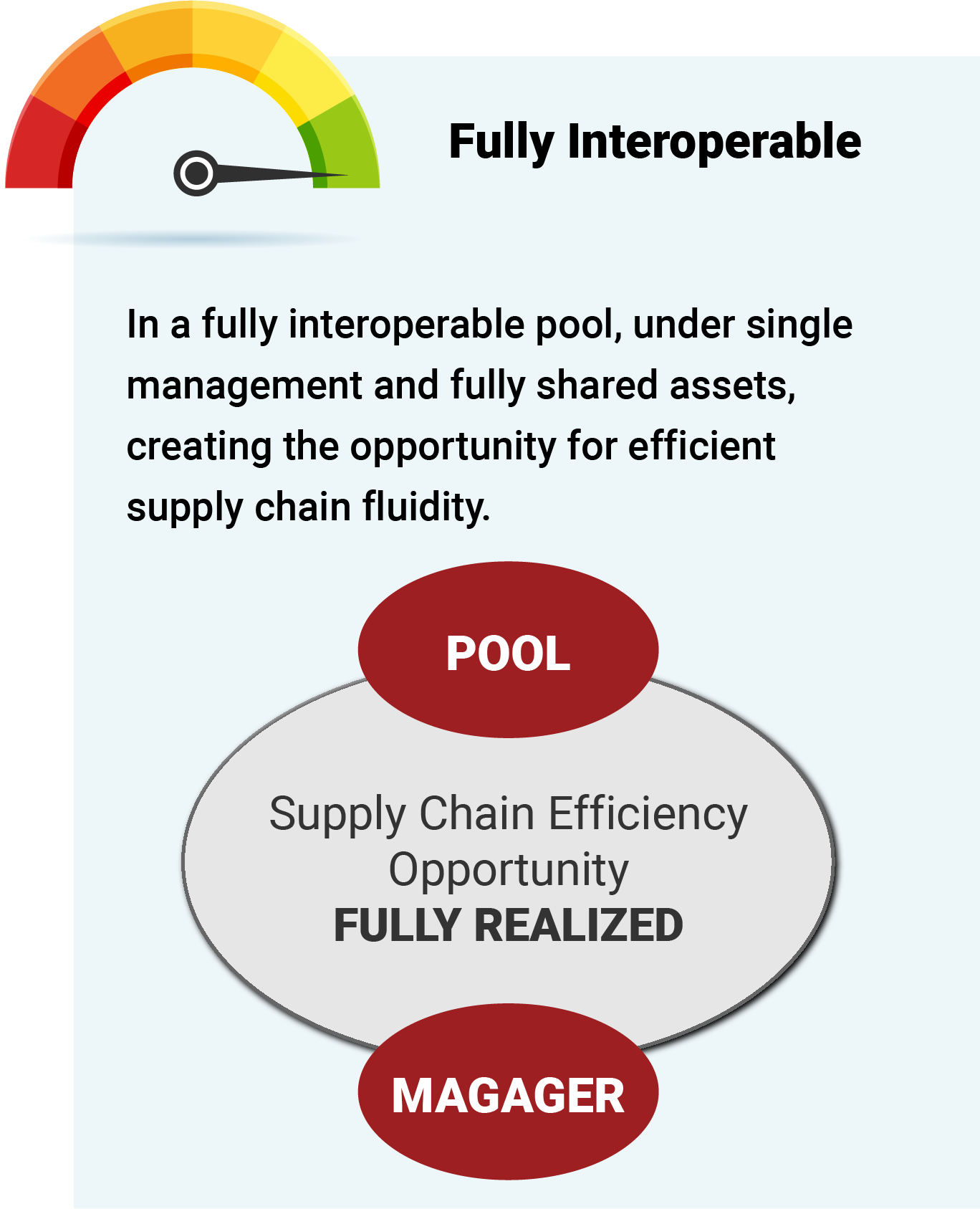