The Management Systems
CCM is committed to its goal of providing best in class chassis management service to its membership. Data management plays a key role in the quality of service provided. The Data Quality team at CCM has implemented a variety of controls, and balances across the business processes, thus facilitating the consistent and on time delivery of superior data quality.
Our powerful technology, powered by Consolidated Intermodal Technologies (CIT), is highly configurable to meet your unique business needs within the supply chain supporting small to large organization’s needs with state of the art technology. It is nimble, dynamic and cost effective, designed by our tech experts but meant for supply chain experts.
Chassis MandR Platform
FACILITATING FAST, EFFICIENT REPAIR FLOW, DRIVING COST OUT OF THE PROCESS
Designed to facilitate fast, efficient repair flow, the Chassis MandR Platform, which is fully integrated with CCM’s Chassis Management Application Suite, is an intuitive system for managing maintenance and repair activities. Utilizing proprietary technology, the application, referred to as MandR (Man-Dar), supports an industry-wide collaborative Platform whereby the sharing of vital information becomes a streamlined and seamless process.
MandR features a collection of modules including: Maintenance and Repair, Tariff Management, Job Order Management, DOT/FMCSA Compliance, Reporting, and EDI subsystem. Contact CIT using the form above.
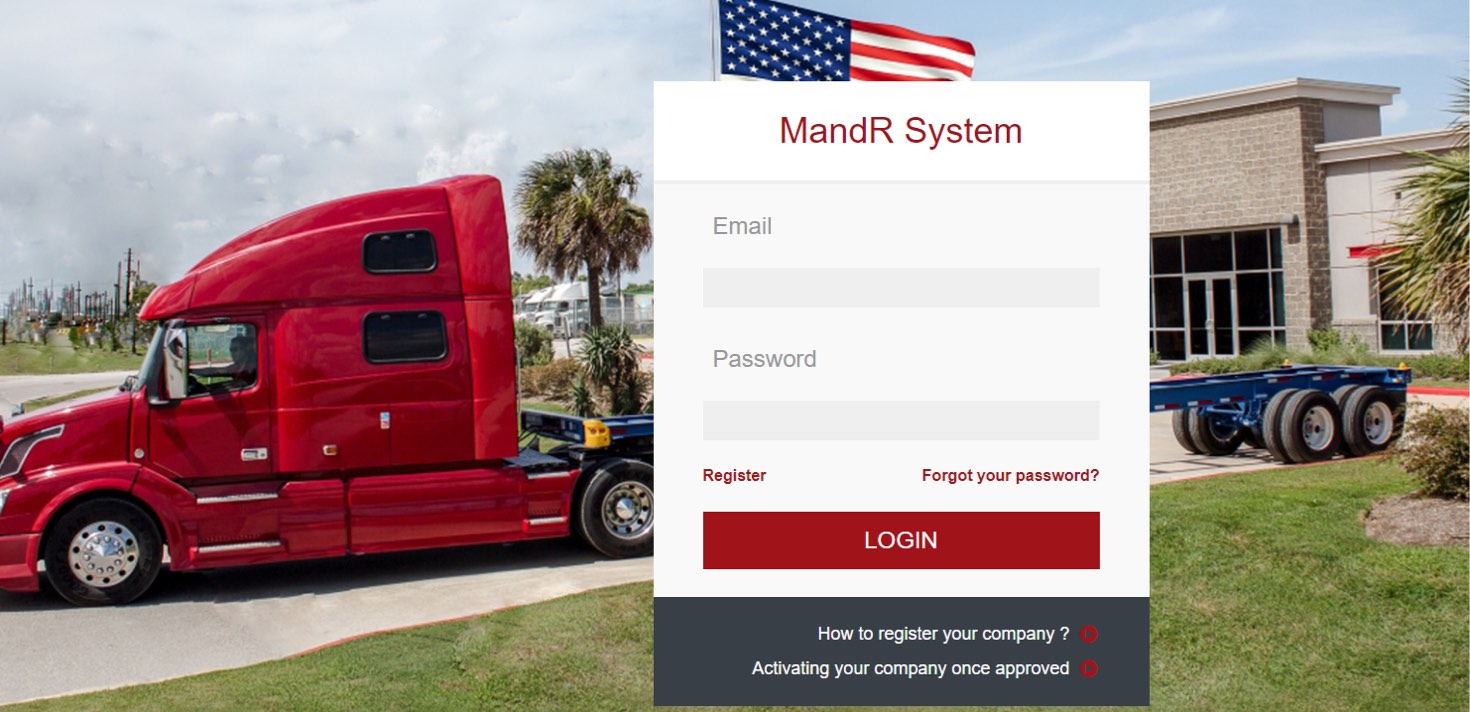
Chassis Management System (CMS)
AN ASSET MANAGEMENT SYSTEM DESIGNED TO REDUCE COST OF OWNERSHIP AND OPERATION
The Chassis Management System Application Integrates near real-time movement data with parameter driven business rules to produce visibility of operations. What’s more, it provides usage billing information to support chassis operations for multiple entities with various roles. CMS is scalable and highly configurable, able to support evolving requirements and adaptations within intermodal freight transport.
The management suite features highly configurable Fleet, Repositioning, Billing, and Reporting Modules
- State-of-the-art web based system managing nearly 90,000 chassis
- Real-time interactive reporting
- Receiving 4.5-6 million transactions in total per month
- Tracking at nearly 300 locations, 400 report variations available
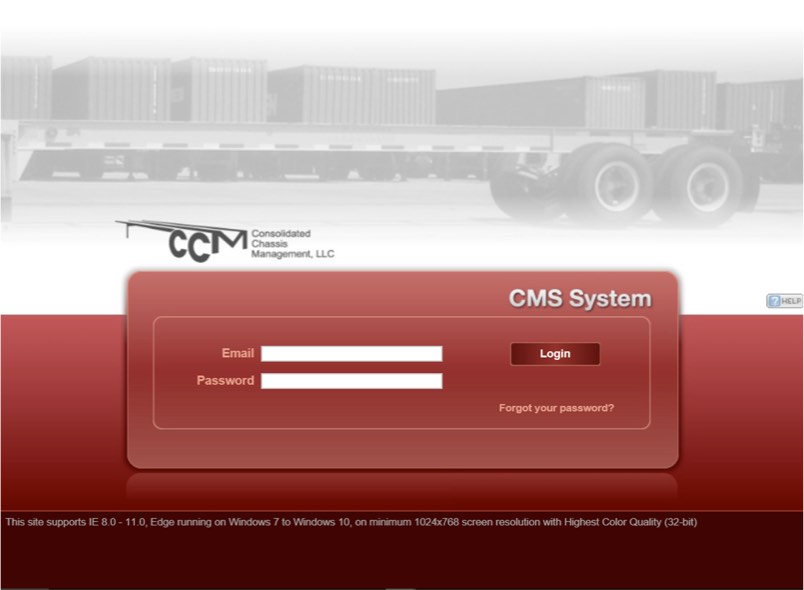
Shipment Management Portal
EXPEDITING AND IMPROVING SERVICE TO THE MOTOR CARRIER COMMUNITY
The Shipment Management Portal replaces numerous manual practices predominantly performed by email, pen and paper, or over the phone. The application suite features four different modules designed to provide quick and seamless processes to gain a chassis booking in co-op or premium pools, manage chassis provisioning, and identify return locations.
- The Booking System Module for coop pools
- The Reservation System Module for premium pool products
- Return Locations Module for chassis, always free, open to everybody, no account required
- Shipment Portal Module; for motor carriers and BCO’s to manage their billing options
Would you like to learn more about how Consolidated Intermodal Technologies can help power your fleet? Contact CIT below for more information:
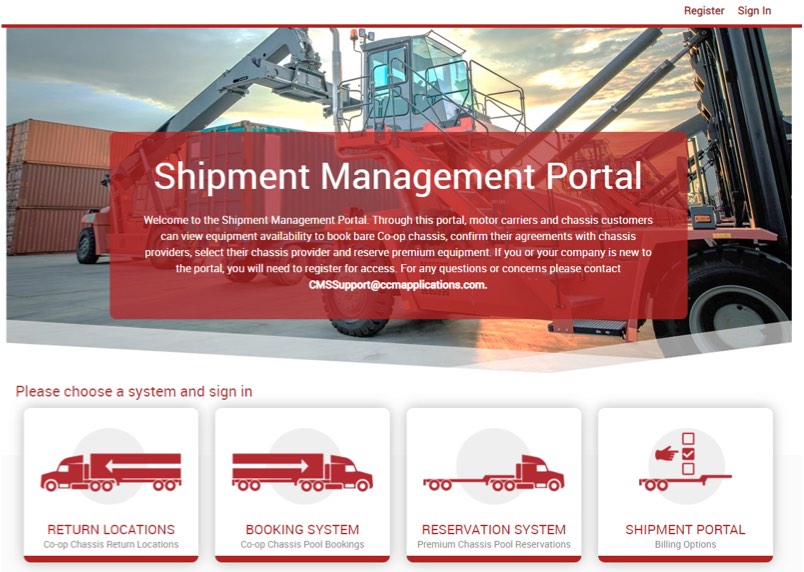